Apply for Exam
| Exam Info
| Recertification
| Benefits
| Procedures
| Cost
Which exam is right for me?
| Certified Professionals
| Show Schedule
| Questions?
Click a menu item to see the corresponding information
Machinery Lubrication Engineer
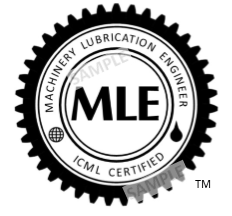 To become certified, an individual must meet the following requirements: - Education and/or Experience - Candidates must have at least 5 years’ education (post-secondary) or on-the-job training in one or more of the following fields: engineering, mechanical maintenance, maintenance trades, lubrication, oil analysis and/or condition monitoring (mechanical machinery).
- No engineering degree or ICML certifications are pre-requisites to candidacy for the MLE certification. However, the MLAs and MLTs would support a candidate’s preparation for the MLE test.
- Examination – Each candidate must successfully pass a 150-question, multiple choice Machinery Lubrication Engineer (MLE)® examination that tests the candidate’s mastery of the ICML's Machinery Lubrication Engineer (MLE) body of knowledge. Candidates have four hours to complete the closed-book examination. A score of 70% is required to pass the examination and achieve certification. Please Note: Due to the four-hour length of this exam, it may impact exam sessions when administered alongside our other exams. Candidates should contact us well in advance to ensure sufficient arrangements can be made.
The MLE Body of Knowledge (BOK) is a structured delineation of the Major Subjects (numbered in bold) that one should master in order to pass the MLE certification exam. The bulleted listings under each Major Subject are examples of the subtopics that help define range and scope. However, the listed subtopics should not be assumed to be complete or comprehensive. Additionally, many subtopics relate to more than one Major Topic and are replicated accordingly.
The BOK is intended to relate to practical knowledge needed by lubrication and reliability engineers who work in user organizations with lubricated physical assets. It is not intended to be academic, scientific or theoretical. The MLE BOK was also constructed to align, at a higher level, to all major BOK subjects across MLA I, II & II and MLT I & II categories and levels. As such, training related to those certifications would support a candidate’s preparation for MLE testing. Most significantly, the MLE BOK is specifically designed to align to the majority of the compliance elements of the new ICML 55 certification for asset management related to lubricated machines. ICML 55 is further aligned to all of the main and relevant subjects required for ISO 55000 certification.
The MLE Body of Knowledge is an outline of concepts that one should have in order to pass the exam. References from which exam questions were derived (Domain of Knowledge) can be found under each area of the BOK.
I. Asset Management, ISO 55000 & ICML 55; Basic Elements (3%) - Definition of Asset Management in the context of the organization
- ISO 55001 Requirements (refer also to EN 16646 for physical assets)
- Physical asset hierarchy (ISO 14224:2016)
- ICML 55 Attributes and Requirements in the context of machinery lubrication
References: - Physical Asset Management Handbook, 4th Edition, John S. Mitchell, Reliability Web; chapters 1-10, chapter 18
- ISO 55000 (International Organization for Standardization)
- EN 16646
- ICML 55
II. Machine Reliability; Basic Elements (5%) - Reliability philosophies and strategies
- Condition-based maintenance (see also Major Subject 4.0)
- Reliability culture
- Financial analysis and economic justification
- Failure Modes Effects Analysis (FMEA), Failure Reporting, Analysis and Corrective Action System (FRACAS), and Root Cause Analysis (RCA) (see also Major Subject 16.0)
- Asset design change process and management of change
- Criticality analysis and risk management
- Metrics, KPIs, Scorecard, Overall Equipment Effectiveness (OEE)
- Asset life cycle engineering and management
- Design for reliability, operability and maintainability
- Managing Sources of vibration and wear, including fasteners, alignment and balance
References: - The Practical Handbook of Machinery Lubrication, R. Scott, J. Fitch, L. Luegner; chapter 2
- Oil Analysis Basics, J. Fitch & D. Troyer, 2nd Edition, Noria - chapter 2
- An Introduction to Machinery Reliability Assessment, 2nd Edition, Heinz P. Bloch, Gulf Publishing Co.; chapters 2-10
- Machinery Oil Analysis, L. Toms, 3rd Edition, STLE; chapter 2
- Reliability-centered Maintenance, 2nd Edition, John Moubray, Industrial Press; chapters 1-8
III. Machine Maintenance; Basic Elements (5%) - Procedure-based maintenance and standardized work
- PM optimization
- Work management, planning and scheduling
- Shutdown, turnaround and outage management
- Operator-driven maintenance, autonomous maintenance, Total Productive Maintenance
- Enterprise Asset Management (EAM) and Computerized Maintenance Management System
- Stores, parts and inventory management
- Workforce management, skills and training
References: - Oil Analysis Basics, J. Fitch & D. Troyer, 2nd Edition, Noria; chapter 2
- Maintenance and Reliability Best Practices, Ramesh Gulati, Industrial Press, 2009; chapters 1-12
- Machinery Oil Analysis, L. Toms, 3rd Edition, STLE; chapter 2
- Preventive Maintenance, T. Wireman, Industrial Press, 2008; chapters 1-11
- Maintenance Work Management Processes, T. Wireman, Reliability Web; chapters 1-9
- The Handbook of Maintenance Management, 2nd Edition, Joel Levitt, Industrial Press; chapters 1 - 29
- Maintenance Planning and Scheduling Handbook, 3rd Edition, Doc Palmer, McGraw Hill; chapters 1-12
- Results Oriented Reliability and Maintenance Management, IDCON
IV. Condition-based Maintenance (CBM); Basic Elements (5%) - Condition-based maintenance versus breakdown maintenance
- Predictive maintenance
- Proactive maintenance
- Inspection 2.0
- CBM technologies (lubricant analysis, vibration, thermography, acoustics, motor current, etc.)
- CBM for major machine categories: pumps, compressors, turbines, gearboxes
- CBM integration and program management
- CBM data management
References: - The Practical Handbook of Machinery Lubrication, R. Scott, J. Fitch, L. Luegner; chapters 1-2
- Oil Analysis Basics, J. Fitch & D. Troyer, 2nd Edition, Noria; chapters 2
- Reliability-centered Maintenance, 2nd Edition, John Moubray, Industrial Press; chapters 7-9
- Results Oriented Reliability and Maintenance Management, IDCON
V. Tribology, Friction, Wear, and Lubrication Fundamentals; Basic Elements (5%) - Mechanical friction, fluid friction, dry friction
- Lubrication fundamentals
- Lubrication regimes, thick film, hydrodynamic, elastohydrodynamic, boundary
- Film thickness, specific film thickness, mixed film
- Film strength, additive and chemical-induced films
- Corrosive, cavitation and erosive wear
- Mechanical wear, abrasion, adhesion, surface fatigue
References: - Lubricants and Lubrications, Theo Mang and Wilfried Drexel, Vol I & II, 3rd edition, Wiley-VCH, 2017; chapter 2
- The Practical Handbook of Machinery Lubrication, R. Scott, J. Fitch, L. Luegner, chapters 2 and 28
- Oil Analysis Basics, J. Fitch & D. Troyer, 2nd Edition, Noria, chapter 1
- Practical Lubrication for Industrial Facilities, H. Bloch, 3rd Edition, CRC Press, 2016; chapter 1
- Lubrication for Industry, K. Bannister, 2nd Edition, Industrial Press, 2007; chapter 3
- Machinery Oil Analysis, L. Toms, 3rd Edition, STLE; chapter 6
VI. Lubricant Formulation for Machine Types to achieve Optimum Reliability, Energy Consumption, Safety and Environmental Protection; Basic Elements (5%) - Liquid and grease lubricants, formulation science, base oils, common thickeners, common additives
- Solid-film lubrication and types
- Physical and chemical properties of lubricating oils and grease.
- Common lubricant laboratory test methods such as oxidation stability, viscosity index, film strength, rust suppression, air release, demulsibility, penetration number, dropping point, water washout resistance, biodegradability, etc.
- Differences and unique physical and chemical properties of major lubricant formulation categories including: engine oil, automatic transmission fluid, brake fluid, hydraulic fluid, turbine oil, gear oil, compressor lubricant, chain lubricant, wheel bearing grease, chassis grease, electric motor bearing grease, coupling grease, multipurpose grease, foodgrade lubricants
References: - Lubricants and Lubrications, Theo Mang and Wilfried Drexel, Vol I & II, 3rd edition, Wiley-VCH, 2017; chapters 4-6, 9-13, 16, and 18
- Handbook of Lubrication and Tribology, George Totten, Volume I, 2nd Edition, Taylor & Francis; chapters 1-11, 13, and 15
- Chemistry and Technology of Lubricants, Roy M. Mortier, 3rd Edition, Springer; chapters 1-14
- Lubrication and Maintenance of Industrial Machinery, R. Gresham and G. Totten, CRC Press, 2009; chapters 2-3
- Fuels and Lubricants Handbook, G. Totten, ASTM International, 2003; chapters 9-17, 20, 24, 25, and 37
- The Practical Handbook of Machinery Lubrication, R. Scott, J. Fitch, L. Luegner; chapters 3-8 and 12-20
- Oil Analysis Basics, J. Fitch & D. Troyer, 2nd Edition, Noria, chapter 1
- Lubricating Grease Guide, 4th Edition, NLGI; chapters 1-4 and 6
- Practical Lubrication for Industrial Facilities, H. Bloch, 3rd Edition, CRC Press, 2016; chapters 4-9, and 15
- A Comprehensive Review of Lubricant Chemistry, Technology, Selection, and Design, Syed Rizvi, ASTM International, 2009; chapters 1-5 and 7-10
- Lubrication Fundamentals, D. Pirro, 3rd Edition, Marcel Dekker, 2016; chapters 2-6
- Machinery Oil Analysis, L. Toms, 3rd Edition, STLE; chapter 3
VII. Job- and Task-based Skills/Training related to Lubrication and Reliability by User Organizations (4%) - Skills possibly required for common tasks performed by lubrication technicians
- Skills possibly required for common tasks performed by operators and inspectors
- Skills possibly required for common tasks performed by mechanics and millwrights
- Training and knowledge required by reliability engineers and maintenance supervision
- Training and knowledge required by plant management
- Standardized training, tasked-based training and competency testing for practitioners in the lubrication field, ISO 18436
References: - Maintenance and Reliability Best Practices, Ramesh Gulati, Industrial Press, 2009; chapter 10
- Preventive Maintenance, T. Wireman, Industrial Press, 2008; chapters 5-6
- Operator-Driven Reliability, T. Wireman, Reliability Web; chapter 7
- Training Programs for Maintenance Organizations, T. Wireman, Industrial Press; chapters 1-11
- Training and Skill Requirements for Lubrication Programs, Edited by Jason Sowards, Reliable Plant Management Series, Noria
VIII. Lubrication Support Facilities needed in Plants and Work Sites (3%) - Design and use of a lube room facility that meets reliability, safely and environment requirements
- Design and use of lubricant storage facilities including bulk tanks, tank farms, totes, etc. that meet reliability, safety, environment and regulatory requirements
- Standardized lubricant labeling for packaged and bulk vessels
- Proper selection, use and care of tools for inspection and reconditioning of tank, vessel and containers related to cleanliness, cross contamination, bottom sediment and water, and leakage
- Spill containment and leak protection practices for environmental protection and basic regulatory compliance
- Transfer, handling, dispensing, filtration from drums, totes and day tanks.
- Transfer, handling, dispensing, filtration from bottles, jugs, and small grease packages
- Selection and use of workplace and lube room tools and accessories (tools, benches, rooms, lockers/cabinets, etc.) and basic care and storage
- Safety practices related to the storage and handling of lubricants
References: - Handbook of Lubrication and Tribology, George Totten, Volume I, 2nd Edition, Taylor & Francis; chapter 34
- Lubrication and Maintenance of Industrial Machinery, R. Gresham and G. Totten, CRC Press, 2009; chapter 7
- The Practical Handbook of Machinery Lubrication, R. Scott, J. Fitch, L. Luegner; chapter 24
- Lubricating Grease Guide, 4th Edition, NLGI; chapter 8 and 10
- Lubrication for Industry, K. Bannister, 2nd Edition, Industrial Press, 2007; chapter 8
- Lubrication Fundamentals, D. Pirro, 3rd Edition, Marcel Dekker, 2016; chapter 20
- Lubricant Storage and Handling, Edited by Jason Sowards, Reliable Plant Management Series, Noria
IX. Risk Management for Lubricated Machines; Basic Elements (4%) - Basic elements of Reliability-centered Maintenance (RCM)
- The Pareto Principle and its application to establish maintenance strategy and focus of resources
- Failure patterns and Weibull Distributions basic elements
- Ranking of lubrication-specific failure modes and causes and the use of Failure Modes Effects Analysis (FMEA)
- Assessment of equipment to determine failure probability along with the severity/consequence of failure
- Basic elements in use of Hazard Analysis Critical Control Point (HACCP) (ISO 22000) to localize and control risk in lubricant-dependent machines and systems
Reference: - An Introduction to Machinery Reliability Assessment, 2nd Edition, Heinz P. Bloch, Gulf Publishing Co.; chapters 3-10
X. Optimum Machine Modifications and Features Needed to Achieve and Sustain Reliability Goals (5%) - Optimum selection, set-up and use of lubricant application devices and hardware (single-point autolubers, circulating lubrication, constant-level oilers, centralized lubrication systems, mist systems, spray, etc.)
- Optimum selection, installation and use of contamination control devices/hardware (filters, breathers, filter cart connects, headspace management, seals, dehydrators, de-aeration devices, etc.)
- Instrumentation requirements including selection and location of online oil analysis sensors
- Optimum selection, location and use of sight glasses and level gauges
- Optimum selection and use of relubrication and oil change hardware & tools
- Optimum selection and location of sampling valves and hardware
- Purpose and use of drip pans, grease traps, berms, purge ports, etc.
- Optimum selection and use of tags, labels and plates for lubricant type and lubrication practices on the machine
References: - Handbook of Lubrication and Tribology, George Totten, Volume I, 2nd Edition, Taylor & Francis; chapter 36
- Lubrication and Maintenance of Industrial Machinery, R. Gresham and G. Totten, CRC Press, 2009; chapter 4
- The Practical Handbook of Machinery Lubrication, R. Scott, J. Fitch, L. Luegner; chapters 9, 10, and 21-23
- Oil Analysis Basics, J. Fitch & D. Troyer, 2nd Edition, Noria; chapter 3
- Practical Lubrication for Industrial Facilities, H. Bloch, 3rd Edition, CRC Press, 2016; chapter 10
- Lubrication Fundamentals, D. Pirro, 3rd Edition, Marcel Dekker, 2016; chapter 9
- Machinery Oil Analysis, L. Toms, 3rd Edition, STLE; chapter 5
- Modifying Machinery for Proper Lubrication, Edited by Jason Sowards, Reliable Plant Management Series, Noria
- The Lubrication Engineers Manual, 4th Edition, AISE, 2010; chapter 12
XI. Lubricant Selection for Optimum Reliability, Safety, Energy Consumption and Environmental Protection based on Machine Type and Application (4%) - Vendor selection based on product range, product quality, product performance, support & services
- Elements in generic lubricant specifications for common machine types, application types, operating conditions, workplace exposures, desired machine reliability, safety requirements, energy conservation, environmental protection and price. Common machine or application types include engines, driveline components, rolling-element bearings, journal bearings, enclosed & open gears, mechanical couplings, process pumps, hydraulic systems, compressors, gearboxes, turbines, chain and wire rope, and pneumatic systems. Lubricant specification elements include base oil, additives, thickeners, performance properties, physical properties, chemical properties, and health and safety properties.
- Food grade lubricant selection, application and regulations related to National Sanitation Foundation (NSF), Food Safety Modernization Act (FSMA), ISO 22000 (HACCP), ISO 21469 and similar guidelines
- Rationalized lubricant consolidation to optimize the number of lubricant grades and brands
- Lubricant cross-contamination risks, compatibility testing, and risk-management practices
- Proper labeling methods using standardized classifications and visual identification system for display on machines, containers, grease guns, lubricant transfer system, etc. Standardized classifications relate to internal and industrial standards including ISO 15380, ISO 12924/6743/12925 and many others related to engine oils, transmission fluids, axle lubricants, and brake fluids. These also include ILSAC, ACEA, API and SAE.
References: - Lubricants and Lubrications, Theo Mang and Wilfried Drexel, Vol I & II, 3rd edition, Wiley-VCH, 2017; chapters 9-13 and 16
- Handbook of Lubrication and Tribology, George Totten, Volume I, 2nd Edition, Taylor & Francis; chapters 1-11, 13, 15, and 25
- Chemistry and Technology of Lubricants, Roy M. Mortier, 3rd Edition, Springer; chapters 8-14
- Fuels and Lubricants Handbook, G. Totten, ASTM International, 2003; chapters 12-17 and 20
- The Practical Handbook of Machinery Lubrication, R. Scott, J. Fitch, L. Luegner; chapters 12-20
- Practical Lubrication for Industrial Facilities, H. Bloch, 3rd Edition, CRC Press, 2016; chapters 11-13, 16 and 17
- A Comprehensive Review of Lubricant Chemistry, Technology, Selection, and Design, Syed Rizvi, ASTM International, 2009; chapter 10
- Lubrication Fundamentals, D. Pirro, 3rd Edition, Marcel Dekker, 2016; chapters 7-8 and 10-15, 17, and 18
- Lubricant Selection, Edited by Jason Sowards, Reliable Plant Management Series, Noria
- ISO 22000
XII. Lubrication-related Planning, Scheduling and Work Processing (4%) - Routine scheduled work and PMs
- Unplanned and condition-based work request processing
- Work prioritization and planning
- Work kitting, matching skill competencies to tasks, assembly of work crews
- Work scheduling
- Unplanned and planned work backlog management
- Process for troubleshooting faults and anomalies (see also Major Subject 16)
- Record keeping, documentation, CMMS
References: - Handbook of Lubrication and Tribology, George Totten, Volume I, 2nd Edition, Taylor & Francis; chapter 33
- Maintenance and Reliability Best Practices, Ramesh Gulati, Industrial Press, 2009; chapters 3-10
- Preventive Maintenance, T. Wireman, Industrial Press, 2008; chapters 2-4 and 7-10
- The Handbook of Maintenance Management, 2nd Edition, Joel Levitt, Industrial Press; chapters 30-39
- Maintenance Planning and Scheduling Handbook, 3rd Edition, Doc Palmer, McGraw Hill; chapters 1-12
- Maintenance Planning and Scheduling, IDCON, Rev. 2, 2008
XIII. Periodic Lubrication Maintenance Tasks (4%) - Control of correct lubricant supply: oil level, flow rate, drip rate, mist rate or grease volume
- Regrease, oil top-up and oil change frequency and lubricant volume (amount) criteria
- Proper oil top-up procedures for common machine types, sumps and reservoirs
- Proper grease relubrication procedures for common machine types and grease dispensing hardware
- Lubricant drain or purge criteria and methods for major machine types
- Contamination control tasks including general machine cleanliness, control of contaminant ingression, filtration, dehydration and other decontamination methods
- Machine flushing requirements, risks and benefits. Selection of flushing protocol, hardware and methodology
- Oil reclamation need and methods (see Major Subject No. 21 below)
- Lubricant waste handling, disposal and cleanup
- Leak detection, management and leak cleanup
- Safety in lubrication maintenance tasks
References: - The Practical Handbook of Machinery Lubrication, R. Scott, J. Fitch, L. Luegner; chapters 9-10 and 25
- Lubricating Grease Guide, 4th Edition, NLGI; chapter 5-7
- The Lubrication Engineers Manual, 4th Edition, AISE, 2010; chapter 13
- Lubrication for Industry, K. Bannister, 2nd Edition, Industrial Press, 2007; chapters 5, 6 and 8
- Lubrication Fundamentals, D. Pirro, 3rd Edition, Marcel Dekker, 2016; chapter 8
- Lubricant Storage and Handling, Edited by Jason Sowards, Reliable Plant Management Series, Noria
- Lubrication Maintenance Tasks and Tools, Edited by Jason Sowards, Reliable Plant Management Series, Noria
XIV. Inspection of Lubricated Machines for Optimum Reliability, Safety, Environmental Protection and Condition Monitoring (5%) - Inspection personnel and responsibility (recognizing this vary between operators, lube technicians, mechanics, and reliability engineers)
- Inspection intervals, routes, autonomous inspection
- Selection and installation of machine inspection windows
- Selection, use and care of inspection tools and aids
- Inspection protocol for common machine types related to start-up, machine-run conditions, machine-stop conditions, repair inspection
- Inspection protocol for spare parts, stored new machines and standby machines
- Inspection personnel skill sets and training
- Inspection checklists, findings reports and documentation
- Integration of inspection with other condition monitoring practices
References: - The Practical Handbook of Machinery Lubrication, R. Scott, J. Fitch, L. Luegner; chapters 21-23
- Preventive Maintenance, T. Wireman, Industrial Press, 2008; chapters 4-6, 9, 18(Append. A, B, & C)
- Reliability-centered Maintenance, 2nd Edition, John Moubray, Industrial Press; chapter 9
- Autonomous Maintenance for Operators, The Japan Institute of Plant Maintenance, CRC Press; chapters 1-4
- Operator-Driven Reliability, T. Wireman, Reliability Web; chapters 5-8
- Preventive Maintenance/Essential Care and Condition Monitoring, IDCON, 1992; chapter 2
- Results Oriented Reliability and Maintenance Management, IDCON
- Daily One-Minute Lubrication Inspections and Field Tests, J. Fitch & R. Scott, Noria
XV. Lubricant Analysis and Condition Monitoring for Optimum Reliability Objectives (8%) - Selection of optimum sampling tools/devices, sample point location(s), sampling frequency, and procedure for common machines, operating conditions and reliability objectives
- Selection of off-site laboratory requirements based on instrument/sample prep capabilities, industry orientation, quality, turnaround time, data reporting format and data interpretation capabilities
- Selection of onsite testing tools/laboratory requirements
- General in-service lubricant sampling and analysis program design
- New lubricant receiving requirements: testing, inspection and quality control
- Stored lubricant (package & bulk) sampling and analysis
- Selection of routine lubricant test slate and standardized methods
- Selection of exception tests, condition for use and standardized methods
- Selection of data alarms and limits
- General strategy for data interpretation
- Data management and overall program management
- Reporting and responding to non-conforming data
- Integration with other inspection and condition monitoring methods
- Accuracy and quality verification and accreditation (e.g., ISO 17025)
References: - Lubricants and Lubrications, Theo Mang and Wilfried Drexel, Vol I & II, 3rd edition, Wiley-VCH, 2017, chapter 18
- Chemistry and Technology of Lubricants, Roy M. Mortier, 3rd Edition, Springer; chapter 16
- The Practical Handbook of Machinery Lubrication, R. Scott, J. Fitch, L. Luegner; chapter 27
- Oil Analysis Basics, J. Fitch & D. Troyer, 2nd Edition, Noria; chapters 4-7
- Machinery Oil Analysis, L. Toms, 3rd Edition, STLE; chapters 7-11
XVI. Fault/Failure Troubleshooting, Root Cause Analysis (RCA) and Remediation (5%) - Basic problem troubleshooting procedures and guidelines
- Application of failure management and processes, e.g., the use of FRACAS policies (Failure Reporting, Analysis and Corrective Action System)
- General RCA policies and guidelines
- RCA phases: data collection, assessment, corrective action, inform and follow-up
- Data collection and evidence preservation policies
- Root cause assessment methods: fault trees, cause-and-effect, sequence of events, etc.
- Guidelines for responding to root cause conditions
- Guidelines for responding to incipient failure/faults
- Guidelines for responding to Impending/precipitous failure
- Sudden-death or catastrophic failure guidelines
- Guidelines for fault/failure findings from rebuild shops
References: - The Practical Handbook of Machinery Lubrication, R. Scott, J. Fitch, L. Luegner; chapter 29
- Lubricating Grease Guide, 4th Edition, NLGI; chapter 7
- Root Cause Analysis, R. Latino, 4th Edition, CRC Press, 2011; chapters 1-11
- Root Cause Failure Analysis, K. Mobley, Newnes, 1999; chapters 1-6 and 19-30
- Reliability-centered Maintenance, 2nd Edition, John Moubray, Industrial Press; chapter 8
XVII. Supplier Compliance/Alignment and Procurement of Services and Products (3%) - Supplier and service-provider alignment/commitment to reliability, safety, energy consumption, quality and environmental protection goals
- Incoming lubricants, parts, and machine product acceptance testing/inspection
- Certificate-of-analysis of lubricant supplies
- Internal/external cleanliness and packaging of new or rebuilt components/parts. Roll-off cleanliness of final machine assemblies.
- Lubricant supply agreement terms and conditions related to quality and services provided
- Supplier safety and lubricant quality communications and documentation
- Services of off-site service providers and rebuild shops (quality, part cleanliness, roll-off cleanliness, documentation, findings reports, etc.)
Reference: - Lubricant and Lubrication Product Procurement, Edited by Jason Sowards, Reliable Plant Management Series, Noria
XVIII. Waste and Used Lubricant Management and Environmental Compliance (3%) - Disposal of lubricants, filters, rags, containers
- Cleaning of containers, parts, hoses, components and devices
- Labeling and documentation of hazardous waste and non-hazardous materials
- Disposal of hazardous and non-hazardous materials
- Alignment to ISO 14000
References: - Lubricants and Lubrications, Theo Mang and Wilfried Drexel, Vol I & II, 3rd edition, Wiley-VCH, 2017; chapters 7-8
- Chemistry and Technology of Lubricants, Roy M. Mortier, 3rd Edition, Springer; chapter 15
- Lubrication and Maintenance of Industrial Machinery, R. Gresham and G. Totten, CRC Press, 2009; chapters 8-10
- A Comprehensive Review of Lubricant Chemistry, Technology, Selection, and Design, Syed Rizvi, ASTM International, 2009; chapter 13
- Lubricant Waste and Disposal, Edited by Jason Sowards, Reliable Plant Management Series, Noria
- Lubrication Fundamentals, D. Pirro, 3rd Edition, Marcel Dekker, 2016; chapter 21
XIX. Energy Conservation and Environmental Protection (3%) - Influence of lubricants and lubrication on energy conservation
- Influence of lubricants on atmospheric contamination
- Environmental-friendly lubricants (e.g., biodegradability)
- Lubricant aqueous toxicity, risk and assessment
- Organizational goals and policies related conservation and protection of the environment
- Optimized and practical use of lubricants and lubrication conservation and environment protection
References: - Lubricants and Lubrications, Theo Mang and Wilfried Drexel, Vol I & II, 3rd edition, Wiley-VCH, 2017; chapter 7
- Chemistry and Technology of Lubricants, Roy M. Mortier, 3rd Edition, Springer, chapter 15
- Lubrication and Maintenance of Industrial Machinery, R. Gresham and G. Totten, CRC Press, 2009; chapter 8
- A Comprehensive Review of Lubricant Chemistry, Technology, Selection, and Design, Syed Rizvi, ASTM International, 2009; chapter 13
- Lubricating Grease Guide, 4th Edition, NLGI; chapter 9
XX. Health and Safety (3%) - Disposal & waste management
- Safety training, policies and guidelines
- Hazardous lubricants and toxicity
- Microbial safety risks and control of transmission (to other machines)
- Fluid pressure and fluid injection risks (blood stream injection)
- Lubricant mists in the work environment
- Confined space risks
- Fire and combustion risks
- Electrocution risks
- Other mechanical risks
References: - Lubricants and Lubrications, Theo Mang and Wilfried Drexel, Vol I & II, 3rd edition, Wiley-VCH, 2017; chapter 7
- Lubrication Fundamentals, D. Pirro, 3rd Edition, Marcel Dekker, 2016; chapter 20
- The Lubrication Engineers Manual, 4th Edition, AISE, 2010; chapter 11
- Lubrication Program Safety, Edited by Jason Sowards, Reliable Plant Management Series, Noria
XXI. Oil Reclamation, Decontamination, De-varnishing & Additive Reconstruction (3%) - Lubricant conservation strategy and practices related to extended lubricant service life
- Selection of dehydration methods and practices
- Additive reconstruction of aged or damaged lubricants
- De-varnishing of fluids and machine surfaces
- Acid scavenging methods, best applications and risks
References: - Practical Lubrication for Industrial Facilities, H. Bloch, 3rd Edition, CRC Press, 2016; chapter 19
- Machinery Oil Analysis, L. Toms, 3rd Edition, STLE; chapters 5, 6 and 10
- Methods for Extending Lubricant Service Life, Edited by Jason Sowards, Reliable Plant Management Series, Noria
XXII. Lubrication during Standby, Storage and Commissioning (2%) - Special lubrication requirements related to machine commissioning and running-in conditions
- Special lubrication-related practices to protect machines and parts in storage or standby
Reference: - Lubrication Requirements for Standby and Stored Machinery, Edited by Jason Sowards, Reliable Plant Management Series, Noria
XXIII. Program Metrics (5%) - Fundamental elements in metrics and performance measures
- Micro metrics of machines and lubricant conditions
- Macro and big-picture metrics for overall fleet or plant machine health
- Mapping and aligning metrics to Return on Net Assets (RONA)
- Overall Equipment Effectiveness (OEE) (related to asset utilization)
- Leading metrics that predict future conditions or events (what’s going to happen)
- Lagging metrics that report or summarize past conditions or events (what just happened)
- Overall lubrication performance and compliance metrics related to cleanliness compliance, lubricant health and PM compliance
- Lubricant consumption ratios/metrics
- MTBF and general machine reliability metrics
- Route compliance measurement
- Percent planned maintenance, workforce efficiency, wrench time
- Metric communication
- Performance control and remediation
References: - Maintenance and Reliability Best Practices, Ramesh Gulati, Industrial Press, 2009; chapters 6-9
- Reliability-centered Maintenance, 2nd Edition, John Moubray, Industrial Press; chapter 14
- Physical Asset Management Handbook, 4th Edition, John S. Mitchell, Reliability Web; chapter 9 and (Append. E)
- Lubrication Program and Reliability Metrics, Edited by Jason Sowards, Reliable Plant Management Series, Noria
XXIV. Continuous Improvement (4%) - Culture of continuous improvement
- Improved Data Analytics (to Industry 4.0)
- Improved CBM sensor application and scope
- Improved cost reductions
- Improved production output
- Improved energy consumption
- Improved environmental protection
- Improved safety
- Improved product quality and timely delivery
- Improve profitability
References: - Physical Asset Management Handbook, 4th Edition, John S. Mitchell, Reliability Web; chapters 1-10 and 18
- ISO 55000 (International Organization for Standardization)
- EN 16646
- ICML 55
Domain of Knowledge
- Rizvi, S.Q.A. (2009). A Comprehensive Review of Lubricant Chemistry, Technology, Selection, and Design, ASTM International
- Bloch, H.P.; Geitner, F.K. (1994). An Introduction to Machinery Reliability Assessment, 2nd Edition, Gulf Publishing Co.
- The Japan Institute of Plant Maintenance (1997). Autonomous Maintenance for Operators, Productivity Press
- Mortier, R.M.; Fox M.F.; Orszulik, S.T. (2010). Chemistry and Technology of Lubricants, 3rd Edition, Springer
- J. Fitch, J.; Scott, R. ((2013). Daily One-Minute Lubrication Inspections and Field Tests, Noria Corporation
- Totten, G. (2003). Fuels and Lubricants Handbook, ASTM International
- Totten, G. (2006). Handbook of Lubrication and Tribology, Volume I, 2nd Edition, Taylor & Francis
- Drexel, W.; Mang, T. (2017). Lubricants and Lubrication, 3rd Edition, Vol. 1, Wiley-VCH
- National Lubricating Grease Institute (1996). Lubricating Grease Guide, 4th Edition
- Gresham R.; Totten, G. (2009). Lubrication and Maintenance of Industrial Machinery, CRC Press
- Bannister, K. (2007). Lubrication for Industry, 2nd Edition, Industrial Press
- Pirro, D.M.; Webster, M.; Daschner, E. (2016). Lubrication Fundamentals, 3rd Edition, CRC Press
- Toms, L.A.; Toms, A.M. (2008). Machinery Oil Analysis, 3rd Edition, STLE
- Gulati, R. (2009). Maintenance and Reliability Best Practices, Industrial Press
- Armstrong, P., Idhammar, T (editor) (2008). Maintenance Planning and Scheduling, IDCON, Inc.
- Palmer, D. (2013). Maintenance Planning and Scheduling Handbook, 3rd Edition, McGraw Hill
- Wireman, T. (2015). Maintenance Work Management Processes, Volume 3, Reliability Web
- Fitch, J.; Troyer, D. (2010). Oil Analysis Basics, 2nd Edition, Noria Corporation
- Wireman, T. (2014). Operator-Driven Reliability, Volume 6, Reliability Web
- Mitchell, J.S. (2012). Physical Asset Management Handbook, 4th Edition, Reliability Web
- Bloch, H., Bannister, K (2017) Practical Lubrication for Industrial Facilities - 3rd Edition. The Fairmont Press, Lilburn, Georgia, USA
- Wireman, T. (2008). Preventive Maintenance, Volume 1, Industrial Press
- Idhammar, I; Et Al. (1992), Preventive Maintenance/Essential Care and Condition Monitoring, IDCON, Inc.
- Moubray, J. (1997). Reliability-centered Maintenance, 2nd Edition, Industrial Press
- Idhammar, C. (2006). Results Oriented Reliability and Maintenance Management, IDCON, Inc.
- Latino, M.A.; Latino, R.J.; Latino, K. (2011). Root Cause Analysis, 4th Edition, CRC Press
- Mobley, R.K. (1999). Root Cause Failure Analysis, Newnes
- Joel Levitt, J. (2009). The Handbook of Maintenance Management, 2nd Edition, Industrial Press
- AISE (2010). The Lubrication Engineers Manual, 4th Edition
- Scott, R.; Fitch, J.; Luegner, L. (2012). The Practical Handbook of Machinery Lubrication, Noria Corporation
- Wireman, T. (2010). Training Programs for Maintenance Organizations, Volume 5, Industrial Press
- EN 16646
- ICML 55
- ISO 55000 and ISO 22000 (International Organization for Standardization)
- Lubricant and Lubrication Product Procurement, Edited by Jason Sowards, Reliable Plant Management Series, Noria. This booklet draws from these "Machinery Lubrication Magazine" articles:
- Why Lubricant Supply Contracts No Longer Go to the Lowest Bidder, Jim Fitch, Noria, July 2001
- How to Negotiate a Lubricant Supplier Agreement, Noria, July 2009
- Buyer Beware: Check New Lubricant Deliveries for Quality, Harold Matroni, Alcoa Mill Products, Sept. 2006
- How Lubricant Suppliers Impact Machine Reliability, Noria, Dec. 2013
- 40 Helpful Guidelines for Purchasing Lubricants, Ken Brown, Utility Service Associates, July 2007
- Why You Should Sample and Test New Oil, Noria, Oct. 2013
- Should New Lubricant Deliveries be Tested?, Jim Fitch, Noria, March 2003
- Lubricant Selection, Edited by Jason Sowards, Reliable Plant Management Series, Noria. This booklet draws from these "Machinery Lubrication Magazine" articles:
- Selecting Lubricants Based on Specifications, Alejandro Meza, Noria, Feb. 2016
- Understanding the Changing Requirements for Food-grade Lubricants, Loren Green, Noria, Oct. 2017
- Lubricant Consolidation, Jim Fitch, Noria, May 2011
- How to Determine Grease Compatibility and Why It’s Important, Rich Wurzbach, MRG Labs, Feb. 2017
- Hazards of Changing Lubricant Brands, Jim Fitch, Noria, Dec. 2012
- Advantages of Using Lube Identification Tags, Wes Cash, Noria, April 2015
- Lubricant Storage and Handling, Edited by Jason Sowards, Reliable Plant Management Series, Noria. This booklet draws from these "Machinery Lubrication Magazine" articles:
- Lube Room Essentials and Best Practices, Noria
- Oil Storage, Handling and Decontamination Can Decide Program Fate, Stephen Sumerlin, Noria, Jan. 2011
- Designing the Optimum Lubricant Storeroom, Noria, July 2001
- 10 Ways to Improve Lubricant Storage and Handling, Stephen Sumerlin, Noria, March 2011
- Advantages of Using Lube Identification Tags, Wes Cash, Noria, April 2015
- The Ins and Outs of Lubricant Storage Regulations, Garrett Bapp, Noria, Oct. 2015
- Best Practices for Lubricant Storage and Handling, Frank Godin, EMA Canada, July 1999
- Retooling Your Lubricant Storage and Handling Equipment, Gerry Looman, IFH Group Inc., Jan. 2002
- Bulk Lubricant Storage and Handling, Jim Fitch, Noria, Sept. 2004
- Bulk Lubricant Storage, Noria, July 2006
- Prevent Additive Settling in Stored Oil, Noria
- Look Both Ways Before Lubricating That Machine!, Stephen Sumerlin, Noria, Nov. 2010
- Ban the Can: Sealable, Reusable Oil Containers Are Smarter Option, Jim Fitch, Noria, March 2010
- When and How to Clean a Sealable, Reusable Container, Noria, April 2012
- Lubricant Storage – Don’t Miss Your Opportunities to Improve, Noria, May 2010
- Best Practices for Topping up Small Sumps and Reservoirs, Garrett Bapp, Noria, June 2017
- When to Use Hard-pipe Lubricant Dispensing, Wes Cash, Noria, April 2013
- Lubricant Waste and Disposal, Edited by Jason Sowards, Reliable Plant Management Series, Noria. This booklet draws from these "Machinery Lubrication Magazine" articles:
- Lubrication Maintenance Tasks and Tools, Edited by Jason Sowards, Reliable Plant Management Series, Noria. This booklet draws from these "Machinery Lubrication Magazine" articles:
- The Dangers of Overgreasing, Noria, Nov. 2011
- Manage the Leakage or Manage the Machine, Noria, Nov. 2007
- Strategies to Achieve and Sustain Dry Oil, Jim Fitch, Noria, May 2009
- Controlling Gearbox Contamination, Martin Williamson, Jan. 2002
- Selecting the Best Strategies for a Successful Oil Flush, Jim Fitch, Noria, Sept. 2004
- 11 Tactics for a Strategic Oil Flushing Program, Jim Fitch, Noria, July 2004
- Electric Motor Bearing Greasing and Lubrication, Noria, Nov. 2007
- Anatomy of a Grease Gun, Bennett Fitch, Noria, April 2013
- Best Practices for Topping up Small Sumps and Reservoirs, Garrett Bapp, Noria, June 2017
- 10 Ways to Improve Lubricant Storage and Handling, Stephen Sumerlin, Noria, March 2011
- Ban the Can: Sealable, Reusable Oil Containers are Smarter Option, Jim Fitch, Noria, March 2010
- Lubrication Program and Reliability Metrics, Edited by Jason Sowards, Reliable Plant Management Series, Noria. This booklet draws from these "Machinery Lubrication Magazine" articles (or from other magazines where noted):
- How to Measure Lubrication Program Success, Jeremy Wright, Noria, Oct. 2014
- Does lubrication belong in the CMMS?, Noria (in “Reliable Plant”)
- Olé! Rallying for a New Lubrication Performance Metric, Drew Troyer, July 2002
- How to Measure the Effectiveness of Condition Monitoring, Jim Fitch, Noria, Aug. 2017
- Measuring the Financial Impact of a Successful Lubrication Program, Jeremy Wright, Noria, Aug. 2016
- Think of OEE as overall business effectiveness, Drew Troyer (in “Reliable Plant”)
- RONA and OEE, Tom O’Reilly (in “Reliable Plant”)
- Understanding overall equipment effectiveness, Carl Wright (in “Reliable Plant”)
- The Power of Maintenance KPIs, Darrin Clark, ArcelorMittal USA (in “Reliable Plant”)
- The what, why, how of wrench time, Doc Palmer (in “Reliable Plant”)
- Planned maintenance hours: What’s a good total?, Doc Palmer (in “Reliable Plant”)
- Lubrication Program Safety, Edited by Jason Sowards, Reliable Plant Management Series, Noria. This booklet draws from these "Machinery Lubrication Magazine" articles:
- Lubrication Requirements for Standby and Stored Machinery, Edited by Jason Sowards, Reliable Plant Management Series, Noria. This booklet draws from these "Machinery Lubrication Magazine" articles:
- Protection of Equipment During Storage, Standby and Decommissioning, Heinz P. Bloch, Process Machinery Consulting, Jan. 2003
- Standby Equipment – Dealing with Oil Without Legs, Jim Fitch, Noria, July 2005
- Oil Mist Lubrication – How to Preserve Equipment, Douglas Branham, Lubrication Systems Co., Nov. 2004
- How Oil Quality Changes During Startup, Craig Jennings, TRI Transmission & Bearing Corp., Oct. 2013
- How to Combat Break-in Wear, Wes Cash, Noria, Feb. 2014
- Developing Commissioning Procedures for Hydraulic Equipment, Brendan Casey, Noria, Nov. 2005
- Methods for Extending Lubricant Service Life, Edited by Jason Sowards, Reliable Plant Management Series, Noria. This booklet draws from these "Machinery Lubrication Magazine" articles (or from other magazines where noted):
- Options for Removing Water in Oil, Martin Williamson (in “Practicing Oil Analysis,” July 2003)
- Strategies to Achieve and Sustain Dry Oil, Jim Fitch, Noria, May 2009
- Tricks and Traps of Oil Reclamation, Simon Norton, Rose Foundation, Nov. 2001
- Contamination Control for Extending Fluid Service Life, Puliyur Madhavan & Neal C. Werner, Pall Corporation (in “Practicing Oil Analysis,” March 2005)
- Vacuum Distillation for the Removal of Water and Other Volatile Contaminants, Jim Fitch, Noria (in “Practicing Oil Analysis,” March 2001)
- Managing Industrial Oil – Oil Life Extension and Recycling, Donald Smolenski, General Motors, Nov. 2005
- Turbine Oil Reclamation and Refortification, Robert W. Bowden & William H. Stein, Shell, July 2004
- Effective Varnish Removal from Turbine Lubrication Systems, Khalid Farooq, Pall Corporation, Aug. 2012
- The Varnish Issue: Strategies for Successful Monitoring and Acceptable Levels, Andy Sitton & Thanant Sirisithichote, Focuslab, June 2014
- Best Strategies for Managing Varnish, Bryan Johnson, Palo Verde Nuclear Generating Station, April 2013
- Modifying Machinery for Proper Lubrication, Edited by Jason Sowards, Reliable Plant Management Series, Noria. This booklet draws from these "Machinery Lubrication Magazine" articles:
- Oil Mist-lubricated Pumps and Electric Motors, Chris Rehman & Heinz P. Bloch, AESSEAL Inc., May 2006
- Guidelines for Oil Mist Lubrication, Michael Khonsari, Louisiana State University, & E.R. Booser, Engineering Consultant, Sept. 2005
- Automated Lubrication – Benefits and Design Options, Wayne Mitchell, Lincoln, May 2001
- Centralized Lubrication Systems Product Guide, Steve Cartwright, LubriSource, Inc., July 2002
- Constant-level Oilers, Carolyn Boldt, Oil-Rite Corporation, Nov. 2005
- Add Oil Circulation to Gear and Bearing Sumps for Greater Reliability, Jim Fitch, Noria, Aug. 2013
- How to Spec a Filter Cart, Noria, Jan. 2009
- Tank and Reservoir Level Management, Martin Williamson, Sept. 2002
- Proper Headspace Management Starts with the Right Breather Option, Stephen Sumerlin, Noria, Sept. 2010
- Labyrinth Seals and Lip Seals: An Economic Comparison, Heinz P. Bloch, Process Machinery Consulting, Sept. 2006
- Reducing Gearbox Oil Contamination Levels, Matt Spurlock, Noria
- Strategies to Achieve and Sustain Dry Oil, Jim Fitch, Noria, May 2009
- How Desiccant Breathers Control Contamination, Wes Cash, Noria, Feb. 2012
- Anatomy of a Grease Gun, Bennett Fitch, Noria, April 2013
- The Basics of Used Oil Sampling, Jim Fitch & Drew Troyer, Noria, Sept. 2004
- Getting Machines to the Proper State of Inspection Readiness, Jim Fitch, Noria, Oct. 2016
- Advantages of Using Lube Identification Tags, Wes Cash, Noria, April 2015
- Best Practices for Oil Mist Systems, Noria
- Training and Skill Requirements for Lubrication Programs, Edited by Jason Sowards, Reliable Plant Management Series, Noria. This booklet draws from these "Machinery Lubrication Magazine" articles:
- To Become World Class, Your Facility Needs a Lubrication Skill Development Program, Noria, Sept. 2010
- Lubrication as a Profession, Jim Fitch, Noria, March 2004
- Develop a Corporate Education Master Plan, Jim Fitch, Noria, Oct. 2014
- Training Strategies to Control Contamination, Loren Green, Noria, June 2017
- Elevating the Status of Lubrication Personnel, Tom Hiatt & Wayne Ferguson, Eli Lilly and Company, Sept. 2007
- Education is Key to Get the Most From a Lubrication Program, Jeremy Wright, Noria, April 2012
- The Changing Roles of Lubrication Experts, Noria, Dec. 2014
MLE Certification is valid for three years from the date of issue. Individuals certified as Machinery Lubrication Engineer (MLE)® must recertify their competency every three years. The purpose for recertification is to ensure that certified individuals keep their skills current and up-to-date.
Recertification is achieved by a points system. To recertify by points, individuals must accumulate 15 recertification points over the three-year period and submit a completed application to ICML. Points may be claimed using the following criteria:
Category | Points | Maximum | Documentation | Training | 1 point per day | 10 points | Proof of attendance (certificate or letter from training company on its letterhead) and a copy of the course outline | Employment | 4 points per year | 12 points | Letter from employer, on company letterhead, with title of signer shown | Publication or Presentation | 2 points per article | 6 points | Copy of publication, table of contents of the book, proceedings, magazine or journal in which it was published. Proof of conference presentation | Conference Attendance | 1 point per conference day | 6 points | Proof of attendance (certificate, badge or letter from conference organizer on its letterhead) and copy of program |
Criteria of Acceptability
- Employment - Employment must be in a field related to industrial lubrication and/or oil analysis.
- Training/Conference Attendance – Topics related to oil analysis, lubrication or other topics important to effective equipment maintenance and management.
- Publication/Presentation - Publications (articles, journals, magazines, books, proceeding, etc.) and presentations about a topic within the body of knowledge for oil analysis, lubrication or equipment maintenance or management.
All points must be earned during the time the certification is in effect. Points earned before or after the certification period will not be accepted. Points may be applied to multiple ICML certifications held by the individual, assuming that the points are applicable and approved for each individual recertification.
If a candidate’s only source of recertification points is employment, the extra points required may be earned via participation in employment-related best practices activities, as per below criteria:
- Selection of Lubricants
- Oversees the selection and performance specifications of all lubricants for each machine, assisted by the lubrication engineer, equipment OEMs and lubricant suppliers.
- Establishes grease vs. oil guidelines.
- Ensures lubricants are optimally selected with respect to cost, wear control, energy conservation, safety, quality and environmental factors.
- Ensures that lubricants are compatible with the machine, process fluids and work environment.
- Writes lubricant standards for all lubricant products.
- Implements a lubricant consolidation strategy.
- Is a member of the buying team for selection of lubricant supplier(s).
- Selection of Lubrication Equipment
- Selects oil mist, single-point, centralized (multipoint) and other automatic lubrication equipment for grease and oil.
- Selects oil level control devices.
- Selects sight glasses and BS&W bowls.
- Selects top-up containers and fill port hardware.
- Selects lubricant dispensing equipment.
- Selects grease fittings, tags and grease guns.
- Selects storage room tools and equipment.
- Selection of Contamination Control Products
- Defines fluid cleanliness and dryness targets.
- Selects filter suppliers, filters types and performance specs.
- Verifies that lubricants and additives are compatible with filters and separators.
- Selects breathers and headspace management equipment.
- Selects oil reclamation equipment and/or service providers.
- Selects filter carts and off-line filtration equipment.
- Selects lubricant heaters and coolers.
- Selects sump reservoir flushing and cleaning equipment and/or service providers.
- Management of Lubrication Suppliers and Service Providers
- Oversees quality, service and support provided by all vendors and jobbers for lubricants, filters, lubrication hardware, lubricant disposal services, oil reclamation services, oil analysis services, software and other independent service providers.
- Identifies procedures for receiving inspection of incoming products (including lubricants) and noncomplying conditions.
- Establishes lubrication and contamination control guidelines associated with equipment rebuilders (engines, motors, pumps, gearboxes, etc.).
- Sets up a supplier performance tracking program.
- Routinely communicates supplier performance to purchasing, engineering and management.
- Lubrication PMs and Work Order Management
- Oversees the writing and scheduling of routine lubrication PMs consistent with best practice for each machine including jobs pertaining to oil changes, top-ups, grease gun routes, filter changes and lubrication inspections.
- Oversees staffing and performance of lubrication work orders and other related unscheduled activities.
- Lubrication Procedures
- Writes specific lubrication procedures consistent with best practices for various tasks (scheduled PMs and routine work orders), including:
- Tank/sump flushing and cleaning
- Oil drain interval and criteria (interval-based or condition-based)
- Top-up procedures
- Grease gun calibration
- Handling and storage practices
- Machine inspections
- Contamination control
- Filter changes and used filter inspection
- Grease gun operation (including how much and how often)
- Lubricant Handling, Storage, Consumption and Conservation
- Oversees all lubricant storage room activities and equipment including layout, lube container selection, transfer equipment, pumps and tools, ventilation, funnels and hoses, safety equipment and procedures, housekeeping standards, training, record keeping, etc.
- Responsible for management of lubricant inventories, reorder points, stock rotation, setting of expiration dates, product labeling and incoming delivery inspections.
- Responsible for tracking and management of lubricant consumption including leakage control. Establishes lubricant consumption strategies.
- Responsible for environmental conservation practices including best practices in waste oil and used-filter disposal.
- New Machinery Specifications and Commissioning
- Develops lubrication-related specifications for new machinery, including:
- Identification of all lubrication points, lubricant type, procedure and frequency of relubrication
- Installation of sampling ports and procedure
- Set up of oil analysis testing requirements by machine
- Breathers and vents selection
- Filtration equipment selection
- Level gauges and sight glasses selection
- Flushing ports and quick-connects selection
- Selects specs for reservoir construction, size, baffles and diffusers
- Initial cleanliness/dryness targets
- Training of lubrication technicians on proper PMs and inspections
- Participates in the commissioning of new equipment during break-in and installation of lubrication hardware.
- Outage and Shutdown Activities
- Assists in providing inspections related to lubrication (tanks, gears, bearings, etc.) during outages and shutdowns.
- Participates in outage/shutdown planning and work-order scheduling activities.
- Warranty and Regulatory Compliance Management
- Ensures that machines are lubricated in accordance with OEM warranties.
- Ensures that lubricant warranties are not violated by noncompliant maintenance practices.
- Ensures that warranty claims are submitted for defective lubricants and lubrication equipment.
- Ensures that all lubricants and lubrication practices (including storage, containment and disposal) are in compliance with relevant government agencies and industry and standards organizations, including ISO, EPA, API, NRC and NSF.
- Manpower Planning, Administration, Staff Training and Certification
- Writes job descriptions, defines job skills (skill standards) and defines certification requirements for maintenance employees or onsite contractor personnel working as lubrication technicians, lubricant analysts, lubrication engineers, etc.
- Manages all lubrication and oil analysis direct line reports and job responsibilities, including onsite contractor personnel.
- Conducts quarterly skill development workshops for lubrication technicians and analysts.
- Selects and schedules onsite training programs relating to oil analysis, failure analysis, troubleshooting, lubrication best practices and contamination control.
- Lubrication Information Management
- Supports the selection and management of lubrication software and other information technology products/ processes including data entry, oil analysis software, PdM software, lubrication scheduling software and related CMMS modules.
- Oil Analysis Coordination
- Selects oil analysis laboratory.
- Selects onsite oil analysis instruments.
- Selects oil analysis software and report format.
- Identifies when, how and where samples will be obtained.
- Selects routine oil analysis test slate for each machine.
- Sets oil analysis alarms and condemning limits.
- Defines exception tests and criteria.
- Defines additive reconstruction strategies.
- Performs/coordinates laboratory quality assurance tests.
- Provides data integration and interface to other reliability technology activities including vibration, acoustics and thermography.
- Failure Modes Effects Analysis (FMEA), Root Cause Failure Analysis (RCFA) and Troubleshooting
- Participates in FMEA and reliability centered maintenance (RCM) planning initiatives.
- Participates in RCFA activities relating to failures of grease or oil-lubricated machinery.
- Develops troubleshooting templates and fault trees for common machine conditions. Trains maintenance staff on their use.
- Management Reporting and Performance Metrics
- Defines overall lubrication program goals, budgets and plans.
- Evaluates proposed lubrication capital expenditures using standard economic analysis methods.
- Coordinates annual lubrication audits and benchmarking services.
- Implements overall lubrication effectiveness (OLE) metrics and other key performance indicators.
- Makes routine progress reports to management and maintenance staff.
 | Loading… |
|