Apply for Exam
| Exam Info
| Recertification
| Benefits
| Procedures
| Cost
Which exam is right for me?
| Certified Professionals
| Show Schedule
| Questions?
Click a menu item to see the corresponding information
Varnish & Deposit Identification and Measurement (VIM)
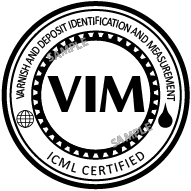 To become certified, an individual must meet the following requirements:
- Education and/or Experience - Candidates must hold either MLA I or MLT I certifications OR have a minimum of 1 year of experience with industrial lubricants and the knowledge base of the Varnish and Deposit Identification and Measurement Body of Knowledge.
- Examination - Each candidate must successfully pass a written, 25-question, multiple-choice examination that evaluates the candidate's knowledge of the topic. Candidates have 45 minutes to complete the closed-book examination. A score of 70% is required to pass the examination and achieve certification.
The Varnish & Deposit Identification and Measurement Body of Knowledge is an outline of concepts that a candidate shall have in order to pass the exam.
References from which exam questions were derived can be found in the Domain of Knowledge.
I. Problems Associated with Varnish and Deposits (20%) A. Flow restriction, starvation and filter plugging B. Restricted movement, stiction and silt lock C. Increased friction and effect on efficiency D. Impaired heat transfer E. Bearing operation F. Need to flush G. Accelerated lubricant degradation H. Lubricant performance properties
II. Varnish and Deposit Composition (24%) A. Lubricant Breakdown Products 1. Oxidation overview a. Mechanism and breakdown products (discuss for base oils and additives) b. Nitration 2. Hydrolysis overview a. Mechanism and breakdown products (discuss for base oils and additives) 3. Thermolysis overview a. Mechanism and breakdown products • Adiabatic gas compression (including dieseling) • Hot wall carbonization (coking and inorganic deposits) • Electrostatic discharge (coking) • Bulk thermal degradation • Combustion from engines B. Contamination 1. Coolants 2. Process chemicals 3. Combustion product/gas blow-by (soot etc.) 4. Cross-contamination (incompatible lubricants, additive precipitation) 5. Vapor phase inhibitor 6. Leached metals 7. NOX Ingression (compressor applications) C. Radiological contamination in nuclear plants
III. How Breakdown Products/Contaminants Become Deposits (24%) A. Solubility of breakdown products: 1. Laws of solubility 2. Polarity. 3. Effect of temperature. 4. Micelle (CMC) 5. Agglomeration 6. Soluble – insoluble equilibria, saturation and impurity-holding capacity (IHC).
IV. Oil Analysis Techniques that can be used to Gauge Breakdown and Propensity Towards Deposit Formation (32%) A. MPC Varnish Potential 1. Test description 2. Importance of sample preparation (omit light, heat 24 hours, incubate 72 hours) 3. Case Studies B. Acid Number 1. Detects oxidation products and hydrolysis products (esters) 2. Varnish precursor and promoter of accelerated breakdown 3. Decrease may indicate additive depletion (spent additives may lead to deposits) C. FTIR 1. Detects oxidation products (varnish precursors) 2. Soot 3. Nitration 4. Sulfation 5. Oxidation 6. Additive Depletion D. RULER 1. Quick evaluation of remaining antioxidant package E. TOST/RPVOT F. ISO 4406 1. soft particle detection G. Panel coker test H. Ultracentrifuge I. Blotter spot test J. Sample physical inspection K. Inspection methods L. OOT/OIT (oxidation onset and induction temperature) M. Noack volatility
Domain of Knowledge - Fuchs, G. H., Diamond, H., “Oxidation Characteristics of Lubricating Oils,” Ind. Eng. Chem., 1942, 34, 927.
- Fitch, J.C. “Using Oil Analysis to Control Varnish and Sludge,” Machinery Lubrication magazine,
- Sasaki, A. “Hydraulic Valve Problems caused by Oil Oxidation Products,” Hydraulic Failure Analysis: Fluids, Components, and System Effects, ASTM STP 1339, G. E. Totten, D. K. Wills and D. Feldmann, Eds., American Society for Testing and Materials, West Conshohocken, PA, 2001.
- Yamaguchi, T., Kawaura, S., Honda, T., Ueda, T., Iwai, Y., Sasaki, A, “Investigation of Oil Contamination by Colorimetric Analysis,”, STLE 2001, San Francisco, California, USA.
- Johnson, M., Livingstone, G. “Identifying varnish and oxidation precursors in lubricant sumps” Tribology & Lubrication Technology, Society of Tribologists and Lubrication Engineers, April 2001, Pages 22-27.
- A. Yano, S. Watanabe, Y. Miyazaki, MHI Ltd, Y. Yamamoto, Kyushu University – “Study on Sludge Formation during the Oxidation Process of Turbine oils” – Tribology Transactions, 47, 111-122, 2004, Presented at the STLE/ASME Tribology Conference, October 2003, Florida.
- Livingstone, G., Thompson, B., Okazaki, M. “Physical, Performance and Chemical Changes in Turbine Oils from Oxidation” Journal of ASTM International, Vol. 4, No. 1, Paper ID JAI100465, ASTM Symposium on Oxidation and Testing of Turbine Oils on 5–8 December 2005.
- Fitch, J. and Gebarin, S., "Review of Degradation Mechanisms Leading to Sludge and Varnish in Modern Turbine Oil Formulations," Journal of ASTM International, Vol. 3, No. 8, 2006, pp. 1-10.
- Fitch, J.C. “What is your Oil’s Impurity Holding Capacity,” Machinery Lubrication Magazine.
- Atherton, B., “Discovering the Root Cause of Varnish Formation,” Machinery Lubrication, March 2007.
- Moehle, W., Gatto, V., Wooton, D., Livingstone, G., “Practical Approaches to Controlling Sludge and Varnish in Turbine Oils”, Proceedings for Lubrication Excellence, May 2007.
- Gato, V., Moehle, W., Schneller, E.R, Cobb, T.W., - “The Relationship Between Oxidation and Antioxidant Depletion in Turbine Oil Formulations with Group II, III and IV Base Stocks,” Journal of Synthetic Lubrication, April/June 2007, Volume 24, Issue 2, Pages 75–124.
- Aguilar, M., Mazzamaro, G., Rasberger, M., “Oxidative Degradation and Stabilisation of Mineral Oil-Based Lubricants,” Chemistry and Technology of Lubricants, Mortier, R. M., Fox, M. F., Orszulik, S. T. Eds., Springer, New York, 2010.
- Hannon, J., “Vanquish Varnish to Improve Gas-Turbine Reliability,” 2011 Outage Handbook – Lubricating/Control Oil, Combined Cycle Journal, 2011.
- Livingstone, G., Ameye, J. “Selecting the Best Varnish Mitigation Technology based on the Application” 2011 Oildoc Conference. Rosenheim, Germany. February 2011.
- Dufresne, P., Hobbs, M. G., MacInnis, G. “Lubricant Varnishing and Mitigation Strategies,” Combined Cycle Journal, Fourth Quarter, 2013, 34.
- Johnson, B., Livingstone, G., Wooton, D., “Root Cause Determination of an Unusual Chemical Deposit on a Key Oil Wetted Component” Proceedings for OilDoc 2013, Rosenheim, Germany.
- Quick, L, Ameye, A., Livingstone, G., “Turbine Oils”, Encyclopedia of Lubricants and Lubrication, Springer Publishing, 2014, pp 2183-2194.
- Hobbs, M. G., Dufresne, P., "Varnish Mitigation: Relative Effectiveness of Non-Deposit-Forming Next Generation Lubricants vs. the Use of Varnish-Removal Filters with their Conventional Counterparts," as presented at LUBMAT 2016, Bilbao, Spain.
- Hobbs, M. G., Dufresne, P., "Why Varnish Removal Fails: The Soluble-Insoluble Varnish Equilibrium," as presented at OilDoc 2017, Rosenheim, Germany.
- Behyan, S., Hobbs, M. G., Kennehpohl, P., Dufresne, P., “Mechanisms of mineral oil-based lubricant degradation and aggregation: towards an understanding of varnish formation,” STLE 2017 Annual Meeting and Exhibition, Atlanta, Georgia, USA.
- Hobbs, M. G., Dufresne, P., “What EHC Fluid Analysis Misses: Improved Phosphate Ester Maintenance Through Non-Routine Testing,” as presented at STLE 2017 Annual Meeting and Exhibition, Atlanta, Georgia, USA.
- Wooton, D., Livingstone, G., "Analysis, Characterization and Sources of Varnish," Proceedings for Reliability World 2007, USA
- Wooton, D., Livingstone, G., "Lubricant Deposit Characterization," Oildoc Conference. Rosenheim, Germany. January 2013.
VIM Badge Certification is valid for three years from the date of issue. Individuals certified for Varnish and Deposit Identification and Measurement must recertify their competency every three years. The purpose for recertification is to ensure that certified individuals keep their skills current and up-to-date.
Recertification is achieved by a points system. To recertify by points, individuals must accumulate 6 recertification points over the three-year period and submit a completed application to ICML. Points may be claimed using the following criteria:
Category | Points | Maximum | Documentation | Training | 2 points per day | 4 points | Proof of attendance (certificate or letter from training company on its letterhead) and a copy of the course outline | Employment | 3 points per year | 4 points | Letter from employer, on company letterhead, with title of signer shown |
Conference Attendance | 1 point per conference day | 3 points | Proof of attendance (certificate, badge or letter from conference organizer on its letterhead) and copy of program | Publication or Presentation
| 2 points per publication/presentation
| 4 points
| Copy of publication, table of contents of the book, proceedings, magazine or journal in which it was published. Proof of conference presentation
|
Criteria of Acceptability
- Employment - Employment must be in a field related to industrial lubrication and/or oil analysis.
- Training/Workshop – Topics related to oil analysis, lubrication or other topics important to effective equipment maintenance and management.
- Conference Attendance - Topics related to oil analysis, lubrication or other topics important to effective equipment maintenance and management.
- Publication/Presentation - Publications (articles, journals, magazines, books, proceeding, etc.) and presentations about topics related to lubrication varnish, such as, detection, formation, control, etc.
All points must be earned during the time the VIM certification is in effect. Points earned before or after the certification period will not be accepted. Points may be applied to multiple ICML certifications held by the individual, assuming that the points are applicable and approved for each individual recertification. If a candidate’s only source of recertification points is employment, the extra points required may be earned via participation in employment-related best practices activities, as per below criteria: - Commissioned flushing
- Identification and prevention of varnish-producing contamination and breakdown products
- Development of lubricant formulations
- Development of lubricant specifications
- Lubricant testing (on varnish or related issues)
- Management of varnish and deposits removal programs
- Root cause analysis or deposit failure analysis
- Varnish and deposit prevention best practices
- Varnish and deposit problems identification and measurement prevention activities
- Varnish and deposit root cause analysis
- Varnish mitigation project
 | Loading… |
|